AI use cases for the manufacturing industry
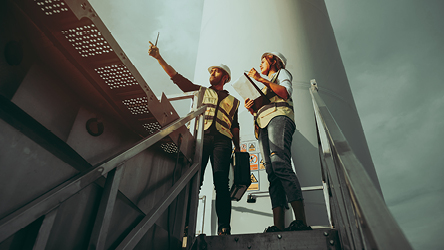
The manufacturing industry generates the most data of all industries, underscoring the sector’s significant impact on the data landscape. To manage and leverage this vast amount of data, manufacturers must adopt AI for practical analysis and utilization.
By exploring AI’s use cases in the manufacturing industry, you can drive innovation and gain a competitive advantage in your industry. We want to help you envision AI’s transformative potential and identify opportunities for strategic implementation.
While the manufacturing industry encompasses an array of business types, we’ve outlined six use cases that broadly apply to most manufacturing operations.
After reading this whitepaper, you have AI strategies to present in the boardroom and demonstrate how different AI use cases can propel your business forward.
Predictive maintenance
Unplanned equipment downtime can severely disrupt production schedules, leading to significant financial losses and delayed deliveries. Based on fixed intervals, traditional maintenance schedules often result in over-maintenance or unexpected breakdowns.
These approaches are inefficient and costly, as they don’t account for the actual condition of the machinery. Unanticipated failures can cause safety hazards and damage to other equipment. To mitigate these risks, manufacturers need a more accurate and efficient method to predict equipment failures.
How can predictive maintenance optimize maintenance schedules?
AI algorithms analyze real-time data from sensors installed on machinery, such as temperature, vibration, and pressure metrics. By identifying patterns and anomalies in the data, AI can predict when a machine will likely fail, allowing companies to schedule maintenance proactively.
This predictive approach reduces downtime and extends the lifespan of the equipment. AI models continuously improve, ensuring maintenance is only performed when necessary, which optimizes resource use and operational efficiency.
“Predictive maintenance is one way AI is helping us improve our manufacturing. So, instead of thinking around stopping lines based on seasonality or needing to do maintenance every month, now we do it when it’s actually needed, which, of course, increases and elevates the productivity of the line.”
Gabriela Cadenas, SVP of Digital and Technology Americas at The Heineken Company (JustDrinks)
What are the challenges to predictive maintenance?
Predictive maintenance (PdM) necessitates collecting and storing vast amounts of equipment data, which requires a robust technological infrastructure to support these activities. Beyond the need for robust data management practices, the nature of this use case can lead to other challenges, such as:
- Demand for specialized knowledge: Successful implementation of PdM demands specialized knowledge in data analytics, artificial intelligence, machine learning, and practical experience with industrial equipment.
- Large volume analysis: Due to the complexity and scale of the information involved, analyzing large volumes of data can be challenging, even with a skilled team of data analysts.
- Security risks: Manufacturing facilities utilizing PdM face heightened security risks, such as ransomware attacks, which pose new challenges for ensuring the safety and integrity of their operations.
AI predictive maintenance: implementation, impact, and key players
Setting up a PdM program can be costly, involving significant investments in sensors, data analytics tools, and the technical expertise to manage these systems.
One vendor that can help with predictive maintenance:
- SenseEye: Nissan uses SenseEye, a predictive maintenance provider, to reduce downtime by up to 50%.
Quality control
Manual inspection processes in manufacturing are time-consuming and subject to human error, leading to inconsistent product quality. The variability in human inspections can result in undetected defects, leading to customer dissatisfaction and increased returns.
As production volumes increase, maintaining high-quality standards becomes even more challenging. Traditional inspection methods also struggle to keep pace with the speed of modern production lines. Ensuring uniform quality across large batches of products is critical for maintaining brand reputation and compliance with industry standards.
How can AI improve quality control?
AI-powered computer vision systems use high-resolution cameras and machine learning algorithms to inspect products for defects in real time. These systems can detect even minor flaws that human inspectors might miss, ensuring greater consistency in product quality.
Companies can also analyze the data collected from these inspections to identify common defect patterns, providing insights for process improvements. By automating quality control, manufacturers can reduce the reliance on manual inspections and improve overall efficiency.
“Each product is thoroughly imaged to detect defects, such as cracks or bubbles in the product, before finalization. If a defect is detected, the product is withheld from delivery. The image is then compared to an external defect image library to identify similarities, helping to determine the cause of the defect. This information can create a ‘digital twin’ of the plant, where an AI model learns about the defect and its origin, ensuring it doesn’t recur.”
What are the challenges to AI quality control?
Again, large volumes of data and mature data management practices are required to ensure these quality control processes work correctly and base their decisions on high-quality, accurate data. Beyond that, some of the other challenges companies face are:
- High upfront costs: The initial investment for high-quality cameras and visual inspection systems can be high.
- Continuous updates and training: AI models require regular updates and training to adapt to new types of defects or changes in product design.
- Integrations: Seamlessly integrating AI systems with existing production lines can be challenging.
AI quality control: implementation, impact, and key players
Let’s turn to some of the world’s biggest manufacturers to hear what they have to say about AI quality control and its benefits:
- Nissan: Employees emphasized the benefits quality control has for their customers:
“With this technology, we’re able to achieve nearly 100 percent accuracy in our inspection process, helping to ensure the customer gets exactly what they ordered.”
Seiji Furuta, a Production Maintenance Specialist at Nissan (Nissan)
- Northvolt: Their gigafactory in northern Sweden introduced a new solution that integrates sensing technology developed internally by their Machine Vision team. It can identify defects at material processing speeds of 50-70 meters per minute in electrode coating production and in less than a second per sheet in stacking. Defective materials are flagged and set aside for manual inspection or scrapping (to be recycled later), reducing scrap costs, decreasing process tuning latency, and enhancing understanding of their manufacturing processes. (Northvolt)
Procurement / Supply chain optimization
Traditional procurement at a manufacturing company involves many manual processes. Procurement officers source suppliers, negotiate contracts, and place orders based on inventory needs and production schedules. They rely on spreadsheets, phone calls, and face-to-face meetings to manage relationships and ensure timely material delivery.
How can AI improve procurement?
AI can enhance procurement at a manufacturing company by automating supplier selection and contract negotiations through data analysis and predictive modeling, ensuring the best deals and timely deliveries. It can monitor inventory levels in real time, predicting future needs and automatically placing orders to avoid shortages or overstocking. Additionally, AI can analyze supplier performance and market trends to continuously optimize procurement strategies, leading to cost savings and increased efficiency.
“Questions such as which raw material to buy; when, where and what is the best route to ship it into the plant; how to efficiently allocate the raw materials to different plants, are best answered by AI models.”
CIO of Tata Steel Jayanta Banerjee
What are the challenges to AI applied to supply chain optimization?
The biggest hurdle for AI-driven supply chain optimization is undoubtedly data quality and management and the amount of data that is needed to build a model because manufacturing requires significant customizations across use cases.. AI models can only perform as well as the data they’re fed, and in the supply chain world, this data often comes from various sources, with differing formats and quality, and can be full of inconsistencies.
Aside from data issues, several other factors can complicate the use of AI in supply chains:
- Integration with legacy systems: Many organizations still use outdated systems that aren’t easily compatible with modern AI technology. Connecting these old systems with new AI tools can be both expensive and time-consuming.
- Change management and adoption: Introducing AI into supply chains often requires overhauling existing processes and workflows. Resistance from employees and stakeholders can significantly slow down or even block the adoption of these new technologies.
- Operational disruptions: AI must be thoroughly designed and tested – if not it can run the risk of making wrong recommendations, delaying schedules, or interrupting the supply chain which can lead to disrupted operations, and ultimately, increased costs.
AI supply chain optimization: implementation, impact, and key players
Improving supply chain processes using AI can reduce inventory holding costs by optimizing stock levels and minimizing overproduction. Predictive analytics can decrease stockouts and overstock situations, ensuring better product availability and customer satisfaction. Enhanced route optimization through AI can reduce transportation costs, leading to faster delivery times and lower fuel consumption.
Research and development
Traditional R&D at a manufacturing company relies on manual experimentation and extensive trial-and-error processes to develop new products and materials. Researchers conduct physical tests, analyze results by hand, and iterate designs based on observed outcomes, often leading to lengthy and costly development cycles.
How can AI improve the R&D process?
AI can enhance R&D in a manufacturing company by optimizing product designs through generative design algorithms, creating multiple design alternatives based on specified constraints and goals.
Machine learning models can also analyze historical data to predict material behavior and performance, aiding in developing new, more durable materials. Prototype development can see improvement as well. AI-driven simulations allow for virtual testing of prototypes, significantly reducing the need for physical trials and accelerating the development process.
Beyond that, predictive analytics can forecast market trends and consumer preferences, guiding the R&D team to focus on innovations with the highest potential demand. Finally, AI can automate routine data analysis and reporting, freeing up researchers to concentrate on more complex, creative tasks.
What are the challenges to applying AI to R&D?
High-quality, comprehensive data is crucial for training AI models. Many manufacturing firms may struggle with fragmented or insufficient data, hindering the development and accuracy of AI solutions. More mature data practices among manufacturers are critical for two key reasons:
- Data silos: Manufacturing firms often store data in isolated systems with varying formats, making it difficult to aggregate and preprocess data for AI applications. Overcoming these silos and achieving data consistency is a significant technical challenge.
- Real time data processing: Implementing AI for real-time applications, such as predictive maintenance or dynamic process optimization, requires the ability to process and analyze data on the fly. This demands robust infrastructure and sophisticated algorithms to handle high-velocity data streams without latency.
AI R&D: implementation, impact, and key players
Traditional methods without AI used to take 20 years, with numerous cycles of trial and error. AI simulations have cut the time down to just two years — 1,000 times faster, a huge improvement in ROI. To see this happen in the real world, look no further than Nissan, one of the largest car manufacturers in Japan:
- Nissan: They applied AI to their car R&D. This process simulates millions of automotive materials and runs tests to predict the ideal properties — strength, temperature sensitivity, conductivity — for their applications.
Customer service chatbots
Handling customer queries manually in manufacturing companies requires significant human resources and can lead to inconsistent service quality and slower response times, especially when dealing with complex technical issues or order specifications.
How can using an AI chatbot improve manufacturing operations?
AI-powered chatbots are revolutionizing the manufacturing industry by enhancing supply management, automating customer support, managing floor operations, providing timely updates, and offering intelligent product recommendations.
Maintaining a steady supply of parts and materials is crucial in manufacturing. AI-powered chatbots provide real-time access to inventory status, reducing waste and ensuring timely order fulfillment. Integrating these chatbots with ERP systems accelerates information retrieval and enables analysis of supply usage patterns, optimizing inventory management through a single interface.
Chatbots can act as virtual agents to facilitate recall procedures and resolve delivery issues. In multi-floor manufacturing plants, they can enhance efficiency by managing floor queries and providing real-time data on workload distribution, production capacity, and maintenance issues.
Finally, AI chatbots assist in product selection using historical data and machine learning to understand customer preferences. They offer personalized product recommendations, enhancing the shopping experience and driving sales. This intelligent capability ensures customers find suitable products quickly, boosting satisfaction and operational efficiency.
What are the challenges to using AI-powered customer service chatbots?
In manufacturing, AI-powered chatbots need accurate and current information about products, services, inventory, and processes to function effectively. If the data is outdated or incorrect, it can lead to wrong responses, frustrated customers, and lost sales. Keeping data up-to-date in a constantly changing manufacturing environment is a continuous challenge that requires regular monitoring and updates.
In addition to data issues, chatbots in manufacturing face other challenges, such as:
- Understanding technical language and jargon: Manufacturing often involves specialized terminology that AI chatbots may not easily grasp. Training these systems to accurately interpret and respond to technical language is a complex and ongoing task.
- Handling complex customer inquiries: Customers in manufacturing frequently have detailed questions about product specs, technical issues, or customized solutions. AI chatbots might struggle with these intricate queries, necessitating human intervention for effective resolution.
- Accuracy and reliability: Keeping chatbots updated with the latest manufacturing techniques and industry standards is essential for providing accurate and reliable advice. Implementing robust error detection mechanisms helps swiftly identify and correct any misinformation. Moreover, involving industry experts to review and validate chatbot responses ensures that the information provided meets high operational standards.
AI chatbots for manufacturing: implementation, impact, and key players
These applications have a relatively low investment cost with the potential for high returns due to savings on operational costs with manual representatives. These tools streamline processes, reduce operational inefficiencies, and enhance overall productivity, making them indispensable assets for modern manufacturing companies.
One vendor that helps with chatbot AI models for manufacturing:
- Cogito AI: MetLife implemented Cogito AI to analyze conversations in real time, which improved first-call resolutions by 3.5% and increased the customer satisfaction score by 13%, all while cutting the average call time in half (Time).
Customer targeting
The legacy approach to customer targeting is labor-intensive, time-consuming, and often lacks the precision and agility that AI-driven methods offer.
How can AI improve customer targeting?
Using AI for customer targeting in a manufacturing company involves gathering data from sources such as order history, product usage patterns, and after-sales service interactions.
AI algorithms segment customers into groups based on purchase frequency, order volume, and product preferences. Predictive analytics identify high-value clients and forecast their future needs, enabling personalized marketing campaigns with tailored offers, such as bulk order discounts or customized product recommendations.
This targeted approach improves customer satisfaction by providing relevant offers and increases sales and customer loyalty by addressing their specific needs.
What are the challenges to using AI for customer targeting?
Inaccurate or incomplete data can lead to flawed customer segmentation, inaccurate predictions, and ineffective marketing campaigns that fail to resonate with the target audience. AI models are only as good as the data they are trained on, and any errors or inconsistencies can significantly impact the accuracy and effectiveness of their predictions.
Beyond data quality, some of the other challenges for AI customer targeting are:
- Data privacy concerns: Handling large amounts of personal data can lead to breaches or misuse.
- Algorithmic bias: AI may inadvertently favor certain groups over others, leading to unfair targeting.
- Over-reliance on AI: Can reduce human oversight, potentially resulting in strategies that lack the nuance and empathy human judgment provides.
AI for customer targeting: implementation, impact, and key players
Harley Davidson recently used Albert (marketing AI) to help improve their customer targeting. They gave the model some of their creative content and performance targets. Analyzing existing data from the dealership, the AI was able to find characteristics of high-value customers within New York. The AI targeted those who completed purchases, added an item to their online cart, or were among the top 25% of people who spent time on the site.
After moving to AI-driven customer targeting, Harley-Davidson New York increased its lead generation by 2930% and opened the company to new audiences it had never previously marketed to.
Data quality as a foundation for AI
Nearly all use cases of AI in the manufacturing industry share a common challenge: the quality of data currently available within the business. Accurate assessments and effective utilization of AI depend heavily on high-quality data. However, many manufacturing companies still struggle with incomplete, inconsistent, or outdated data. To fully harness the potential of AI, decision-makers must prioritize improving data availability and data quality first and foremost. This involves:
- implementing robust data governance practices, which include a catalog of all the data
- investing in advanced data integration and cleaning technologies and data standardization
- fostering a culture that values data accuracy and completeness.
By addressing these foundational issues, manufacturers can leverage AI to enhance quality control, optimize supply chains, and effectively target customers. We at Ataccama are leaders in helping manufacturing companies use high-quality data in a secure and governed way. Download this free ebook to begin building your end-to-end DQ framework.